5-13-10 WOW have I been busy. I really need to work on
this blog to give updates. I have been working hard on some new
molds for the side skirts. I almost have the mold and new model done
for the drivers side scoop. I had my cad drawings done for the metal
braces for the scoops and I am getting bids on the cost to get them
laser cut now. I purchased some 2x4 that I will rip down to make
into a mock up chassis configuration for the LMP3 vehicle. I
purchased another 96 Toyota Camry V6 so now I have 2. So busy all
the time, just the way I like it. I have two people installing the
cables that go with the LETSLA and I am getting good feedback on the
instructions for editing. They should be available soon for sale. My
goal is to go back and edit this years blog to give a better history
of what has happened.
5-3-10- No I am not dead, just a slacker for not updating
this more. We had a nasty snowy winter. Once we came out of it
my project mind went into crazy mode. I made a bike rack for my
Lotus. People think I am crazy, but if it is a nice day I want to
drive my Lotus and also be able to go riding. So now I have both. I
also decided to make some side skirts for the Lotus Elise and some
side scoops. I have the skirts installed. See the blog pictures for
details.
http://www.trueleo.com/blogpictures.htm I also purchased
an vertical end mill. I have been wanting one for a while and found
one on ebay that was a good deal. I went up to NY and picked it up
and came back to VA in one day. What a crazy day. I am going to
update here more and do more details soon. I got a 1964 Austin Mini,
a 1996 V6 Camry and a 1991 MR2NA with a blown motor. I am putting
all three together to make one crazy car once the TRP3 is done. More
to come.
1-11-10 I got word that the axle has been finished
and shipped so I should get it any day now. I also have decided to
use a Kirky 47 series road race seat for the vehicle. The seat I got
from Tillet is a Kart seat so it does not have the seat belt holes
as needed and it is not as comfortable for a long ride as it should
be. The Kirky with the cover comes in different sizes for people
small and larger, is light weight, cost effective and can handle the
elements. Once I get the seat I can work on figuring out the exact
dimensions of the fuel cell since that will be going behind the seat
and will be custom made to fit. One of the other final items I am
still looking for is the supplier for the suspension components and
have a few companies I have contacted that I can work with. Once I
get some more final figures on what I require then I can figure out
who to go with, I just need to know the exact weights on each first.
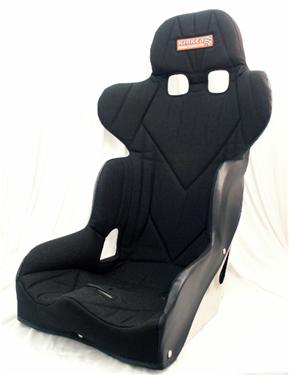
1-5-10 It has been a cold winter so far. I got stuck in
the snow with my Lotus and had to leave it at some random guys house
for a week. Fun. I purchased a 1/10 scale model from Toys-r-us the
other day so I could get the wheels, driver, steering wheel and
other odds and ends to make a 1/10th scale model of the TRP3. I want
to make the model so I can see a realistic representation of what
the chassis will look like when done and then I can start working on
the body. I plan on making the model first and then making the full
size when the chassis is all done. I also plan on make the buck out
of foam and then making a mold from it. The final body will be made
out of carbon fiber. I am scared to think about the amount of time
it will take me to make the buck and get it just right. I have made
molds of items before, but not in the size of a vehicle before. I
will also look at companies that can do it for me if the cost is
good.
12-15-09 I finally got the swingarm in had. It will work,
but is way more robust and large than I thought when designing it.
We have redisgned it and will have it bolt inside instead of outside
of the yellow part in the picture below. This way we can start out
with solid piece of alum that is less than 1/2 the size of the first
on and be less than half the finished weight. This first one will
work on the prototype machine for testing and the final version with
be on production vehicles. I also finally got all the measurements
for the drive axle. I forwarded this to the company that will be
making the custom axles. The only issue is it takes 4 weeks to get
the axles done as they have to make it and send it out to be
hardened. At least we are finally seeing progress here.
11-20-09 Got a call from the CNC shop and they finished
the swingarm. It should be on its way and I should get it after
Thanksgiving.
11-5-09 Finally at SEMA Las Vegas after what felt like an
entire day sitting on plains and in the airport. This place is
amazingly huge. I spent the first day there just walking and
walking. I did find some good contacts I can be using for the
project in the future so the function of going there has been
accomplished.
11-1-09 I awarded the swingarm CNC work to a company in
Arizona. I really liked how professional their shop is and will give
them a chance on the prototype one with the hope of using them for
other parts of the vehicle in the future. I am excited to get this
done. They gave me a date of 11-20-09 for completion. It is crazy in
that they are starting out with a solid billet piece of aluminum
that is $500+ just for materials and then do all the CNC work on it.
It should come out really strong, light and look great.
10-21-09 Good comes from a new design. I had a design
that I came up with for the prototype swingarm in which I would get
some of the parts CNC and then I would TIG weld them all together.
Later in the process I would make it one solid piece and may have it
cast and then machined. I decided to make the entire side piece out
of one solid piece. The material alone cost s a ton, but it will be
worth it to have a product that will resemble what the final product
will be. Here are some teaser photos of it is SolidWorks. I am still
tweaking it so it will be a little different when done.
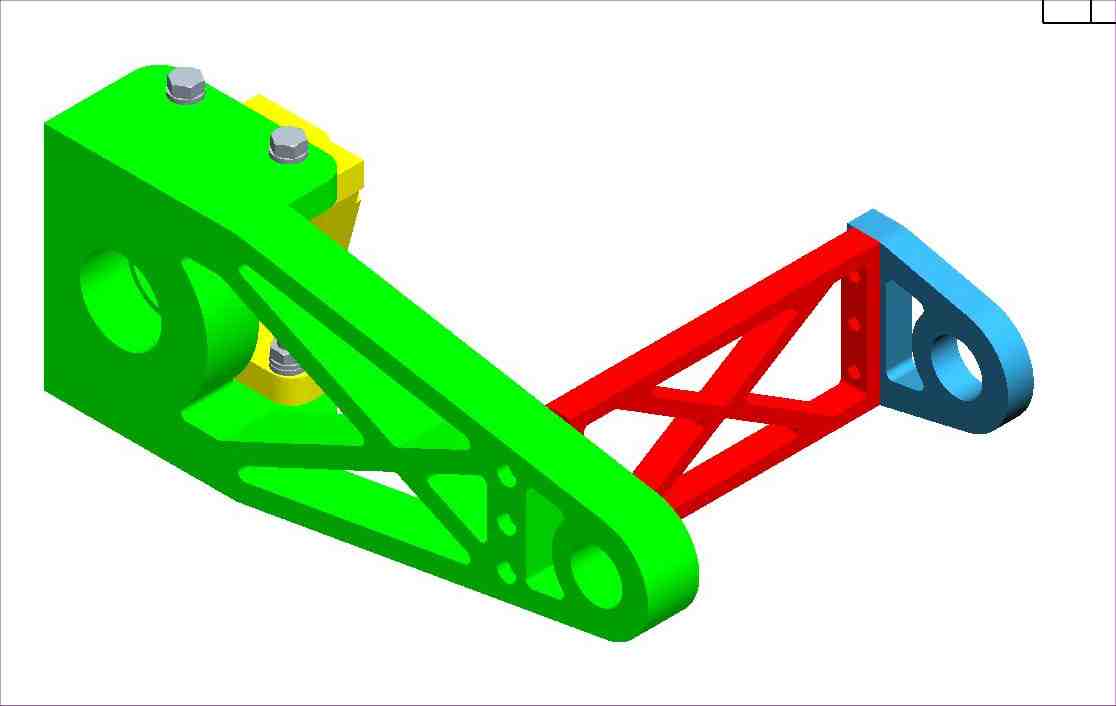
10-18-09 Here is a picture of the wheels I have for it. I am
going to SEMA at Vegas in the first week in Nov and I will be
looking at different suppliers for the wheels. The picture is not
that good and is my iphone. Yet another reason to go out and buy a
new camera. This weekend maybe. These are really nice wheel from
Iforged custom made from forgings to the specs I need and want. The
only problem is that they are megamoney so I am looking for
something that is a little less costly and as light as possible. We
will see what I can fined.
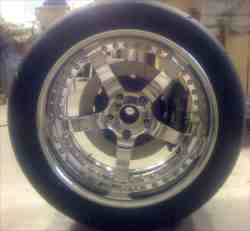
10-15-09 I finally broke down and purchased the new
2009-2010 Solidworks edition. I am looking forward to working with
it myself and learning all the ins and out of it. I will use it to
design the chassis and suspension to start with. I will also take
all the parts that have been made so far and put them together to
make the final fully assembled vehicle. I am excited to say it will
be done in CAD all before. In the end I plan on making the entire
body in SolidWorks and then working with a fluid dynamic engineer to
get maximum downforce.
10-9-09 The Lemons 24 hour race was great. I had a black
flag in my first few laps in they day for passing someone under
yellow, but the in car video shows I did not, ugggg, so I did not
get seat time in the daylight until the very very end. In all it was
so much fun and driving in the dark is an adventure to say the
least. I look forward to the next time I get to race and it will not
come soon enough.
10-2-09- Going to the races. I am going to OH for the
Lemans race. We have a 91 NA MR2 and OMG it is so much fun to race.
10-1-09- Talked with the engineer today about the final
changes to the design before it goes off to the stress analysis
engineer for testing. The stress guy is a specialist in that and
will make sure that it is strong enough to withstand the loads. I am
pretty sure it is as I am overbuilding everything here to just make
sure. My plan is that later I will design to make it as light as
possible when all the testing is done on the prototype.
9-30-09- Made some updates based on the engineers
suggestions to the assembly and sent it back to him.
9-15-09- Sent the engineer the first draft of the
completed rear swingarm design. He will review it and get back with
me when completed. He is about a week out.
History-
Summer 2009
I had to wait a 3 months to finally get the
rims and wanted them before I went and designed the rear swingarm.
While waiting I figured out the front steering system. It was harder
to find specific items for a center mount rack and pinion system
that has the correct rations and size for it. What I found was sand
rail buggy racers use just what I needed. I have the system and it
should work work out great. I also ordered a Tillet T250 seat. It is
super light and fits me well. I wanted a seat that if it gets wets
it will not be a big deal. I may try to find a different seat in the
future, but for now it will work.
I also decided to use round tube chromoly. It cost a lot, but
I think it is worth it to have a chassis that is as strong as
possible for the weight. I was going to use square stock for ease,
but decided to go with round as it is a lot stronger for the weight.
It will take more time to match up, but it will be better in the
end.
I also found it hard to make an axle to adapt a Corvette hub
to a motorcycle sprocket. I did find a company that I am going to
use that makes custom axles and will be using them. It will take
some time, money and effort to get it done, but it should be able to
handle all the hp I throw at it. I just have to get my final
swingarm assembly done up and then I can get the specifics of axle
dimensions.
Right now I am working on the rear swingarm design. I am working
with a mechanical engineer and putting all the CAD designs into
stress analysis to make sure the parts will work together. That
should be done very soon and then I can get the rear swingarm parts
all CNC'ed.
Spring 2009-
Now comes the commitment time to the project.
I went out and purchased a 2000 Suzuki Hayabusa donor bike. I
decided to use this bike because it has a 1300cc 200hp engine and
Suzuki has made about 100,000 of them so parts will be available
easily. I purchased it from an older rider who got a new one and
then never rode the old one. This bike is modified a little bit with
a power commander, exhaust, JE pistons, rods and some other bits
there and there. Needless to say this is way faster than stock and
will do 200+ easy. I did ride it in bike for just one time and it
was so fast it scared the hell out of me so I parked and it left it
there. After feeling the power I knew this would be the correct
engine for the project.
I had the bike and took it apart a little bit. I decided that
I wanted to make sure I got all the bits and parts needed to do the
project before doing major decisions on design. I knew the hardest
thing to design was going to be the rear swingarm and that has
proven so true. I needed a rear single hub that would be strong
enough to handle the 200 hp and possible up to 400hp if I turbo it.
I needed and independent rear end set up and also wanted something
that was available. What I found was that a 2000+ Corvette single
rear would work so I ordered a used set up. I found that I had to
make my own spindle as the stock one would just not work, but I did
use the hub/bearing set up and the rear brake set up from the
Corvette.
Now that I knew what rear brake setup I would use I went to
figuring out the front spindle break setup. I found that Wilwood had
a good setup with the spindle/brake setup that would work. I worked
with them and we designed up a braking system that is specific to
the 3 wheel vehicle. The entire braking system, from the pedals,
master cylinders, spindles, hubs, rotors and calipers are all made
by Wilwood and matched to work just right for this setup. That was a
major hurtle to overcome and work out.
Now that I got the braking system done I could figure out
what wheels and tires to get. I started with the tires and knew what
size I wanted. I went with a 205/40/17 front and 305/35/18 rear. I
wanted to have a smaller front tire and really wide rear tire to
balance out the vehicle. I also read up and found the Toyo R888 had
a great rating and are really grippy. I also found out the hard way
that I could not find a wheel I wanted with the rear size of 18x10
with the 4.5 x 5 bolt pattern and the offset I wanted and also have
a matching front set of 17x7 with a 4.5x5 bolt pattern. What I did
was get a custom forged set made by Iforged. They look really good
and should work well, the only problem is they cost a lot.
Winter/ 2009-
Now that I finally have the LETSLA orders all
filled and the shifter to where I want it to be I went ahead and
started on making my dream vehicle. A quick history on this. Back to
the LMP race cars I really wanted to make one from scratch myself,
but if I did a 4 wheel vehicle and did it all out it would really
just be a track car. I want a vehicle I can drive everyday if I want
and I will want to. I decided to make it 3 wheels with 2 in the
front and 1 in the back. I would make the rear wheel about twice as
wide as the front. I have seen this arrangement in the T-REX from
Campagna in Canada. The only problem when I saw it was that it is
$50,000. I could not afford that and liked the styling a little bit.
So I thought I could make one that fits my style and what I thought
it could be. I could make it just like an LMP race car look, with
stunning performance and have a one off unique vehicle that would be
challenging to make. My targets are 750lbs with 200 hp and
insane handling. Now as soon as I say three wheels people think it
can not be stable and will not handle well, but this is not true.
With 2 wheels in the front it can and will handle very well. After
some drawings and photoshop I came up with the basic look of the
vehicle and now I just need to get on with making it. Sounded easy
in my head, but for each step forward there is always some setbacks.
Fall 2008/Spring 2009-
Since the house is done and I living here I am going to get a
nice sports car. I had an 05 S2000, but it was a lease and was going
back to the dealer Aug 08. I have always wanted to buy a Viper, the
05-09 car. They are just badass with the 8.0 V10. I also liked the
Lotus Elise/Exige. I found a dealer that had a nice 08 Viper in red
and made an appointment to look at the car. I also knew there was a
Lotus dealer on the way in Richmond VA so I made an appointment to
look at one of them on the way. I had never seen one in person and
when I saw the Lotus it looked amazing. I love small little nimble
cars and this fit the bill. The car I drove was an 08 S240 and it
was so nice. I did not buy a car that day, but I knew I wanted a
Lotus and did not even go to drive the Viper. I then started to look
for one and thought it would be better to buy a used one then new
because I planned on tracking the car. I also wanted a supercharged
one and the aftermarket superchargers make more power than the stock
ones. I found a perfect Elise in MD and went up and got it.
The first day I had it I figured out, just like everyone
else, that the shifter simply sucks in the car. It felt like a truck
or worse. The MR2 had way better feel. After looking at it for a
long time I figured out that the problem was with the linkage system
at the transmission. The stock linkage system has plastic bushings,
so much slop in it it just jiggles around and the ratios are made
for a front wheel drive so the throws are long because of that. I
designed multiple versions and finally settle on one that I liked. I
used 4 sealed cartridge bearings and two rod end bearings. I could
not decided on what ratio do finally do so I put in different
threaded holes for the rod ends that would go on it so I could
adjust it later myself. My intent was to fix the shifter in my car
and if I liked it I would try to sell it. I really liked the way it
felt when done and decided to sell it. I knew there was a need, but
did not realize I would sell out my first batch made in the first
week I put them up for sale. Needless to say I was behind in my
orders at the time and finally got them filled. I have since updated
the design to what I call the 2nd generation. This version uses
better rod end bearings that are beefier and some other updated
components.
2008-
My house is finally finish, as I should say I am living in it
and a house is never really done. I still to this day have a list of
little things to do and I plan on doing them someday. Living in the
house I worked on finishing up the shop and getting all my tools and
equipment moved from the old shop. OMG- I never realized how much I
had and how much stuff weights in a shop until you move it all. The
shop is basically divided up into three main areas. Basically half
the bottom is the machine shop area. I try to accumulate tools here
and there and now have just about everything I want and need to
build just about anything. People do ask me if I have a CNC and
never got one because it is easier and cheaper to just outsource all
my CNC work. Maybe someday I will get some CNC machines if the
demand is ever there. The other half of the bottom is two bays and
one has a two post lift in it. Now I do have a bad back and have had
4 back surgeries. It finally feels great now with the last fusion
surgery. The top portion is the loft portion for storage and we call
is Troy's-R-US.
2008 and before-
I have always loved the look of Lemans prototype race cars. I
thought it would be amazing to be able to have one and drive one on
the street, but the truth is it would be so illegal I would not get
very far. So how do I have a LMP car for the street? A good question
I pondered for a long time. About 10 years ago I built a Factory
Five Racing cobra kit car. It was fun and fairly simple to build.
This made me ponder and think that someday I could design and build
my own car and my day dreaming went on for years.
I purchased a 1991 Toyota MR2 around the year 2000. I have
always thought a proper sports car should have the engine in the
middle of the car, but maybe that is because I like F1 to much. On
the way home it overheated from a blown headgasket that took some
time to figure out. While rebuilding it I found some great internet
sites, like www.mr2oc.com and got
to modifying it until it became so extreme it killed the reliability
and fun. I eventually took the car apart and put a stock enging back
and in sold it. During the process of modifying it started to build
parts for others and there formed Trueleo Racing LLC. I made and
sold parts from exhaust to intakes to complete stand alone computer
systems with tuning for MR2's. The basic business model at the time
was to simply enjoy myself making parts and developing new ideas for
the car. I then branched out a little bit and made some intakes and
exhausts for Fiero's and still sell them today as special orders.
In 2005 I started to build my house. I was the general
contractor and did a lot of the work myself. I took pride in the
work and basically put Trueleo Racing on a semi hold status to get
the house done. I did keep it up and going, but could not put the
effort into the business as needed as the house took all my focus.
In building the house I planned on building a shop next to it to
match. I thought it would be great to just to be able to go to the
shop instead of driving around and have everything right there. I am
glad I did it this way now, but someday I plan on getting a really
big shop made. I knew I would put more effort into the business when
done and it is not like a job at all and I enjoy it everyday.
|